For your information
You are being redirected to one of our divisional subsites which contains more detailed information on the required division. To navigate back to the main Invicta Group site, please click the link found in the footer at the bottom of the page.
4 Simple Tips to Make Your Warehouse Space Safer
2nd June 2020
The final frontier
Quick Quote
Contact Mick Coyne
To get a quotation or arrange a free site survey - Call Mick Coyne on
-
UK
Current location:
Quick Quote
Contact Mick Coyne
-
UK
Current location:
Put enough people and products into any room, and it’s bound to throw up a few hazards. This goes double for a warehouse or other storage environment, where people and pallets come and go on a regular basis. The combination of constant movement, vehicles, stacks and shelving creates numerous points of conflict, any of which could easily cause injuries and damage.
Thankfully, there are plenty of ways to address this. While much of it is common sense, all of it stems from proper planning, discipline and training. Applying the following lessons throughout your organisation – and ensuring that they continue to be followed – should serve to make your warehouse space safer, and your employees happier and more productive.
Increase visibility
To recognise a hazard, you have to be able to see it. That seems simple enough, but you’d be amazed at the number of facilities which suffer from inadequate lighting. This is often the result of dated halogen, metal halide or fluorescent lighting solutions, which not only cast an uneven and pallid light, but are also extremely inefficient. Modern LED lights will usually provide better coverage, increasing visibility and saving you money on energy costs.
The presence (and visibility) of signage is also paramount to good safety. Emergency exits should be well-lit and signposted, with signs at intervals to direct anyone who’s not familiar with the building towards the nearest one. Proper floor markings are also important, particularly to delineate areas for vehicles and pedestrians, and warn people where vehicles may be coming around a corner or out of another blind spot.
For the drivers, a system of mirrors will help enormously to spot hazards and act accordingly, as will driver safety signs at loading points. Clearing obstructions is also vitally important, both in and around the aisles; stacks of pallets or even carelessly strewn packaging can impair visibility, and act as a distraction for drivers. This may all sound like common sense, but it’s easy for one lapse to snowball into a major issue, so keeping across it all is key.
Upgrade your racking
Racking often operates beyond its shelf life, and is forced to adapt to all sorts of goods and pallet sizes which it wasn’t designed for. This not only leads to gross inefficiencies, but can also prove to be a health & safety nightmare. Pallets are often overloaded, or placed onto racking not designed to support them, leading to undue stresses on the racking.
Pallets are also frequently not loaded onto racking properly, meaning that items hang over the edges, and could be prone to falling into the aisles. Sometimes there’s simply not enough space in a warehouse or other storage area – particularly at peak times like Christmas – leading to items simply being stored in the aisles. All of these problems pose huge risks to the safety of personnel, whether they are responsible for loading and unloading pallets or picking items.
Whether or not you currently have a high density pallet racking solution, it’s always a good idea to reassess your racking format and layout on an annual basis, in order to ensure that you’re storing goods as efficiently and safely as possible. Ideally you should combine this with a survey of your staff and contractors, getting feedback on areas or processes which might feel dangerous or hazardous, and acting accordingly.
By enlisting the help of a pallet racking specialist, you may be able to unlock additional space within your facility, either through the use of a higher density format or by building upwards, and utilising empty headroom. This will not only ensure that everything is stored safely and securely, but also free up space for additional racking or other uses – enabling you to put off an expensive expansion or relocation.
Practices > PPE
In any industry that involves manual labour, it’s easy for employees to become over-reliant on their sense of skill and experience, and take unnecessary risks. Sometimes this means they don’t bother wearing PPE at all, but more often, it means relying on PPE in the event that something goes wrong. People trust that because nothing bad has happened before, it won’t in the future, and that PPE is their insurance against serious injury.
If we were giving a seminar on health & safety, one of the first lessons would be to never rely solely on your equipment. In industry terminology, PPE is an active protection system, like the role a sprinkler plays in a fire. What you want to do is avoid the fire ever happening in the first place, not rely on your ability to run away from it. As we know, you might not always get the chance.
Instead, you should ensure that safety principles and best practices are instilled into all of your employees and site visitors. This comes down partly to training, but also to constant reinforcement through your internal policies and protocols. By holding people to certain expectations, enforcing routines and conducting regular toolbox talks, you can ensure that hazards don’t crop up in the first place. PPE and other safety equipment is a last resort in the event that your policies fail, not a first point of call to protect you from stupid decisions.
Upskill employees
One of the most common causes of accidents in a warehouse environment is vehicle collisions, due either to a lack of training on the part of the operator, poor warehouse design, or a lack of awareness among pedestrians. The high speed, high pressure environment of logistics can also contribute to these risks, however, making it paramount that everyone has a full understanding of the hazards posed by indoor vehicles, and the best ways to prevent them.
By training as many employees as possible to operate forklifts and other vehicles, you can kill several birds with one stone. By giving all of your employees a better understanding of the vehicles – what their speed is, how they move and operate etc – they can act more appropriately around them, potentially reducing their likelihood of injury. But they will also gain valuable skills that could help them to fill future shortages, and gain a renewed appreciation for the business – potentially increasing their happiness and productivity.
First aid training also a fantastic skill to have, and something you can easily extend to a wide range of employees. While traditional First Aid and Emergency First Aid at Work courses are ideal, you may also wish to consider investing in First Aid for Mental Health training. 1 in 100 adults in the UK now possess some kind of mental health training, allowing them to spot issues with co-workers and offer support. Safety is as much about mental health as physical health, and the two often go hand in hand.
Accreditations & Affiliations
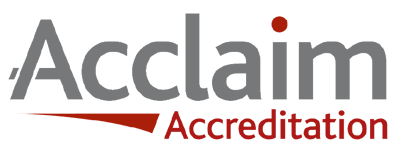
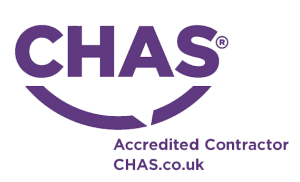
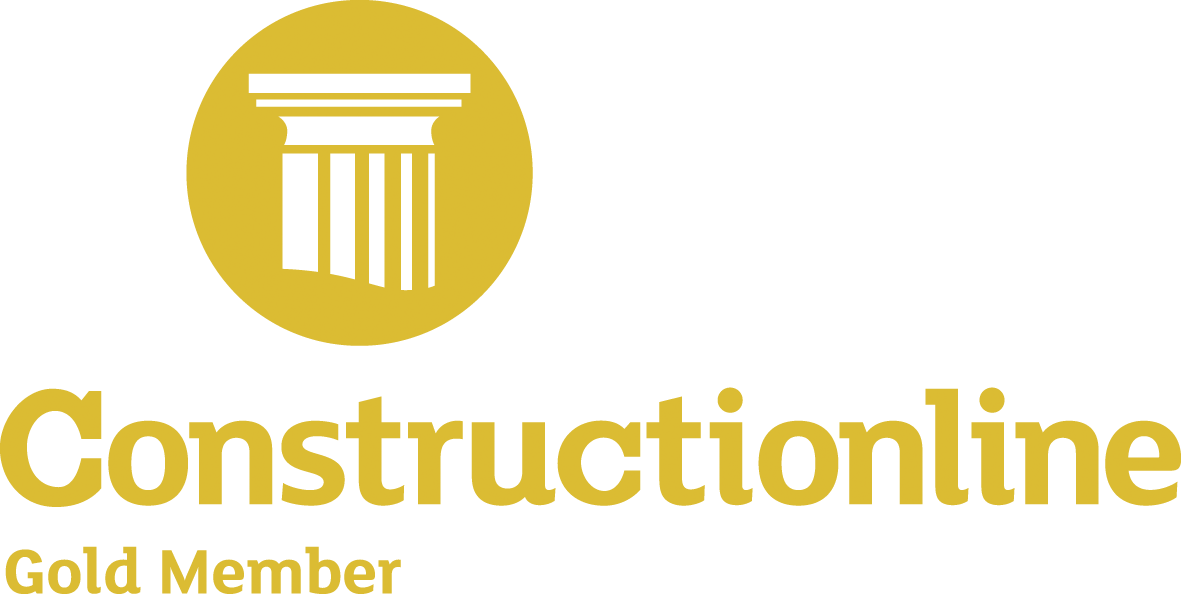
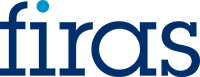

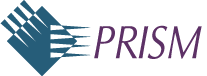
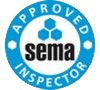
Start your project
Tell us about your project. Please complete this form. One of our sales team will come back to you with more details. If you prefer, you can drop us an email.
Share/Like this page