For your information
You are being redirected to one of our divisional subsites which contains more detailed information on the required division. To navigate back to the main Invicta Group site, please click the link found in the footer at the bottom of the page.
General Racking Inspections and Procedures
7th January 2020
How to ensure your racking is inspected and protected
Quick Quote
Contact Mick Coyne
To get a quotation or arrange a free site survey - Call Mick Coyne on
-
UK
Current location:
Quick Quote
Contact Mick Coyne
-
UK
Current location:
Most businesses recognise the need to carry out regular inspections, as well as the need for constant oversight and vigilance when it comes to racking safety. However, not everyone plans out how they’re going to do this, leading to ad-hoc implementation. This can leave gaps in your safety strategy, potentially exposing you to unnecessary risks.
While the following guide is only a basic overview of the process of organising inspections, it should give you a base from which to build a more comprehensive, coherent strategy. Ideally, you should ensure that you:
Appoint a PRSS
In the same way that you will have appointed a ‘responsible person’ for health & safety oversight, you should appoint what SEMA calls a ‘Person Responsible for Racking Safety’, or PRSS. This individual will bear the brunt of the responsibility for safely operating your warehouse storage, including the organisation of racking inspections, repairs and maintenance, as well as the keeping of accurate and up-to-date maintenance logs.
Like the ‘responsible person’, the PRSS isn’t just there for periodic inspections – they have a range of important ongoing responsibilities. A PRSS needs not only to be able to organise and log inspections, but also to analyse and act on the information they receive, make an assessment on how damage may have been caused, and be given the power to take action to prevent future issues.
Outline a process for immediate inspections
Immediate inspections should be undertaken whenever any damage or fault is reported to your racking, racking accessories or other related components. Warehouse staff should be encouraged to report all incidents, no matter how seemingly small they may be. Racking awareness training can help to instil this, and increase the accuracy of reporting.
An immediate inspection will establish the damage to the specific area in question, document this damage, and flag it for further action if necessary. This record should then be logged and taken into account when further inspections are carried out, or forwarded to the PRSS to plan a course of action and enact maintenance or repairs.
Plan regular inspections
A timetable for regular inspections should be outlined by the PRRS, to be carried out by trained personnel. This should be carried out on a minimum monthly basis, although the actual frequency will be determined by your risk assessments. The PRRS will be responsible for overseeing the process, ensuring that information is collected and logged properly, and that suitable actions are taken.
Actions taken by the PRRS should not only be limited to finding and addressing faults with the racking framework and accessories. The PRRS and inspectors should also seek to establish how damage is occurring and address systemic issues with loading practices. Finally, they should ensure that load notices are present and correct, and that they are being adhered to.
Plan annual inspections
Annual inspections must be carried out by a trained and certified inspector, known as a SEMA Approved Rack Inspector (SARI). As a result, most businesses opt to employ an external inspector to visit their sites and carry out comprehensive inspections. This has the benefit of looking at the racking with fresh eyes, potentially spotting issues you may have missed.
SARI approved inspections can take two forms: a damage-only inspection or a full SARI report. A damage-only inspection will only look for visual defects caused by impact damage or stress, while a full report will carry out more tests and provide more technical detail. While a full report is preferable, your approach may depend on your internal inspection process.
The warehouse should be cleared as much as possible to allow the inspector to fully assess all of the racking, and not have to navigate any clutter. Like the other inspections however, the annual inspection is mostly visual and on the ground level. This may depend on the nature of your racking though, both in terms of how many levels there are and how goods are loaded.
Undertake racking safety awareness and inspection training
In order to instil and enforce proper racking safety, you need to make sure that your workforce is qualified. This usually means providing adequate training to at least one or two people within the warehouse – but the more people you train, the more likely it is that damage will be avoided, and flagged up when it does occur.
A Racking Safety Awareness course is sufficient for regular inspections. These courses teach candidates how to identify faults in various types, formats and configurations of racking, as well as how to log and report them, and what action to take. Invicta Racking offers these courses, and you can find more information on our training page.
Annual inspections tend to be done in slightly more depth, providing more technical information, and so require more specific training. Many businesses choose to outsource their annual inspections, as they are not deemed frequent enough to train an existing employee or to dedicate an entire position to. However, you can opt to send an employee on a SEMA Approved Rack Inspection (SARI) course to learn these skills.
Accreditations & Affiliations
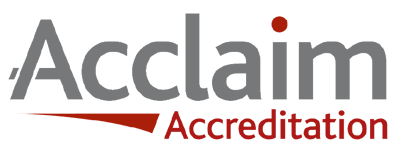
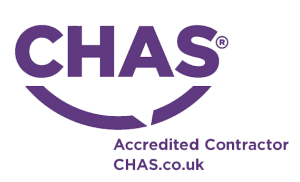
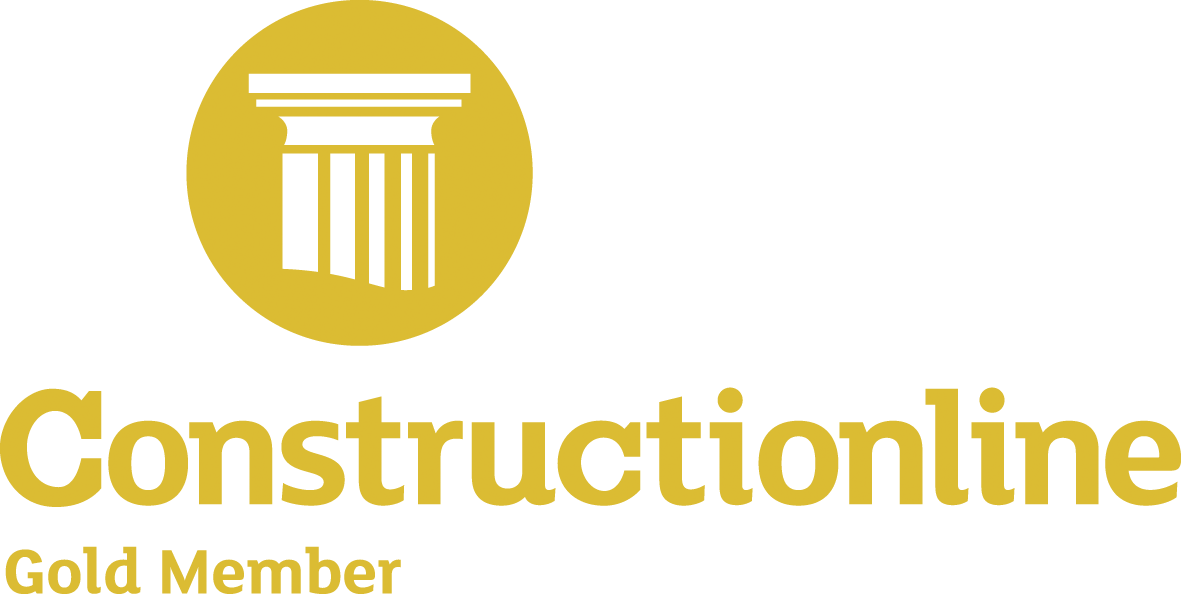
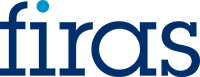

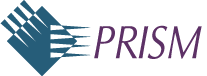
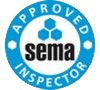
Start your project
Tell us about your project. Please complete this form. One of our sales team will come back to you with more details. If you prefer, you can drop us an email.
Share/Like this page