For your information
You are being redirected to one of our divisional subsites which contains more detailed information on the required division. To navigate back to the main Invicta Group site, please click the link found in the footer at the bottom of the page.
How to make your warehouse storage more flexible
27th March 2023
Quick Quote
Contact Mick Coyne
To get a quotation or arrange a free site survey - Call Mick Coyne on
-
UK
Current location:
Quick Quote
Contact Mick Coyne
-
UK
Current location:
For businesses involved in the ecommerce supply chain, things move quickly. Increasing demand, high turnovers, faster delivery options and variances in item and pallet sizes can all cause serious headaches for warehouse operators. The end result is often that pallets are stored and retrieved inefficiently, or even stacked outside of existing pallet racking.
Thankfully, there are ways that you can make warehouse storage more flexible, and more adaptable to the current e-commerce environment. By making structural and logistical changes, you can adapt your warehouse to better accommodate different types of goods, facilitate faster methods of storage and retrieval, and improve the overall efficiency of your operations.
Boom and bust
Recent years have brought crisis and opportunity in equal measure for the storage and logistics industry. On the one hand, demand skyrocketed for online shopping and home deliveries during the pandemic, and doesn’t seem to have abated. On the other, a range of political and economic factors are hampering the supply of various goods. Storage space is more expensive than ever, and delays mean that some products continue to see shortfalls.
The ecommerce landscape hasn’t just seen an increase in demand. The rise of next-day and same-day delivery has also dramatically reshaped supply chains, with warehouses increasingly being built close to or within urban centres. Combined with transport delays (such as those seen periodically in the Port of Dover) and ongoing paperwork issues, this has seen warehouse space skyrocket in price, and prevented many firms from expanding. The increased cost of trading with the EU has also fallen on businesses, making their offerings less competitive, and in some cases forcing businesses out of the market.
The competitiveness of the jobs market also continues to cause problems. Following on from the well-advertised shortage of HGV drivers (at least partly due to a shortfall in EU labour), warehouses across the UK are now struggling to fill operative roles. This appears to be being driven both by a shallow pool of prospective employees and general competition, with employee wages and perks rising across the sector in a bid to compensate. All of these factors have made the current environment difficult for warehousing and logistics firms, and require novel approaches to remain agile and competitive.
The value of flexibility
While investment can seem counterintuitive at a time of such instability, making your warehouse space more flexible to changes has numerous benefits
The same can be said of stockpiling, which has become increasingly common in recent years in order to smooth over these interruptions. Optimising your warehouse space can make it more efficient and allow you to stockpile more, without having to invest in a costly expansion or an entirely new warehouse. Creating this additional space gives you the flexibility to use it for extra storage when needed, and potentially to adapt it for other uses when the need for stockpiling dies down.
Having the capacity to store and retrieve different pallet and item sizes also insures you against changes in your product lines and consumer demand. If you find that you need to pivot to offering different kinds of items in different quantities, a more flexible warehouse will make this process far quicker and smoother – reducing the time it takes you to react, and giving you a valuable headstart on the competition.
Ways to make your warehouse storage more flexible
Flexibility is a broad term, and there are numerous ways to improve it. Fundamentally, it means making changes that reinforce your warehouse storage against changes in supply and demand, and making it as adaptable as possible to different use cases and different methods of operating. Here are just a few ways to make your warehouse storage more flexible that are easiest to implement, and will deliver the best results.
Invest in high density racking formats
High density pallet racking adds the best and most utilitarian form of flexibility: extra storage capacity. A variety of high density racking formats are available, with the potential to as much as double your storage capacity compared to traditional racking, or halve your current racking footprint. The extra space generated can either be used to store more pallets (or a greater variety of pallets), or to create space for things like production or packing areas.
Cantilever racking can be used to store long and awkwardly shaped objects, while narrow aisle racking can combine with specialised forklifts or autonomous vehicles to provide even denser storage. Modular racking designs also allow for the racking to be easily adapted, expanded, dismantled or moved without compromising its stability or safety – providing the ultimate flexibility for your future storage needs.
Explore autonomous vehicles
Speaking of autonomous vehicles, new developments in AVs and robotics offer excellent potential, both for future-proofing and present-day efficiency savings. New autonomous warehouse vehicles can be integrated with warehouse management systems, allowing them to carry out tasks with minimal intervention. Advanced sensors meanwhile allow them to move around the warehouse without posing a risk to personnel.
The ability of autonomous vehicles to operate independently and carry a variety of pallet sizes and weights allows them to be adapted to different uses. They can be used without an advanced WMS or sensor arrays and can still provide value by automating simple tasks, assisting operatives with manual labour. When you do decide to upgrade your warehouse automation, their potential is unlocked – allowing them to undertake more complex tasks, and act based on data to automatically store and retrieve pallets or items.
Optimise traffic flows
Traffic can often be an invisible bottleneck within warehouses – or at least one that is rarely considered. When demand spikes, traffic around a warehouse can cause delays and exacerbate risks, with vehicles and pedestrians jostling for space, and working in an unorganised manner. This free-for-all leads to valuable time being lost, as queues form unnecessarily, and delays grow as the pressure impedes workers’ performance.
Reconsidering how traffic moves through your warehouse – and instigating some form of traffic control – can protect workers and save money. Collisions are one of the most common types of accident in warehouses, and threaten both racking and personal safety. Using static or active signage, lights or simple rules on navigation can prevent this, reducing damage and absences due to injury. All of this saves money and labour hours – giving you the flexibility to invest it somewhere else.
Consider a warehouse mezzanine
With the price of additional storage space at an all-time high, creating new space within your existing premises is invaluable. While high density pallet racking is one way to achieve this, another is to install a mezzanine floor. By creating a mezzanine above your racking, you can utilise empty headroom in tall warehouse spaces. This not only creates more space for storage or other purposes, but makes more efficient use of your warehouse in terms of HVAC.
Warehouse mezzanine floors can be built to support almost any use case, whether that’s more racking, production or office space, or heavy plant for manufacturing. Like our high density pallet racking, mezzanine floors also have an adaptable and modular design. This ability to extend or relocate, combined with the ability to host various activities, makes them an ideal way to expand your storage footprint or other space rather than having to relocate – giving you the flexibility to react to changes in demand.
–
Having the capacity to adapt to changes in market conditions is invaluable for any warehouse operator, particularly at a time of such global instability. Making your warehouse more flexible through efficiency savings, new technologies and the creation of new space will all put you at an advantage, and give you the ability to react more quickly and effectively to any challenges that lie ahead.
Accreditations & Affiliations
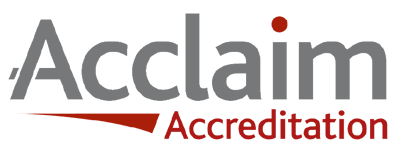
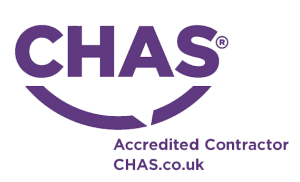
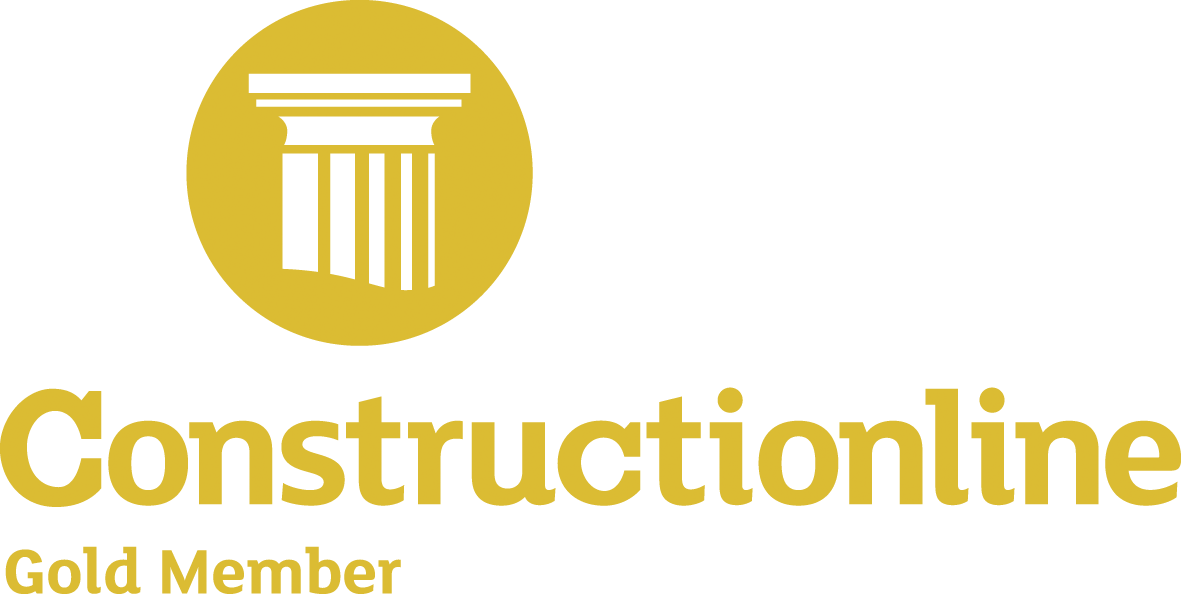
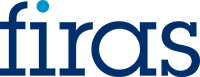

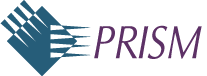
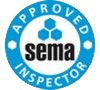
Start your project
Tell us about your project. Please complete this form. One of our sales team will come back to you with more details. If you prefer, you can drop us an email.
Share/Like this page